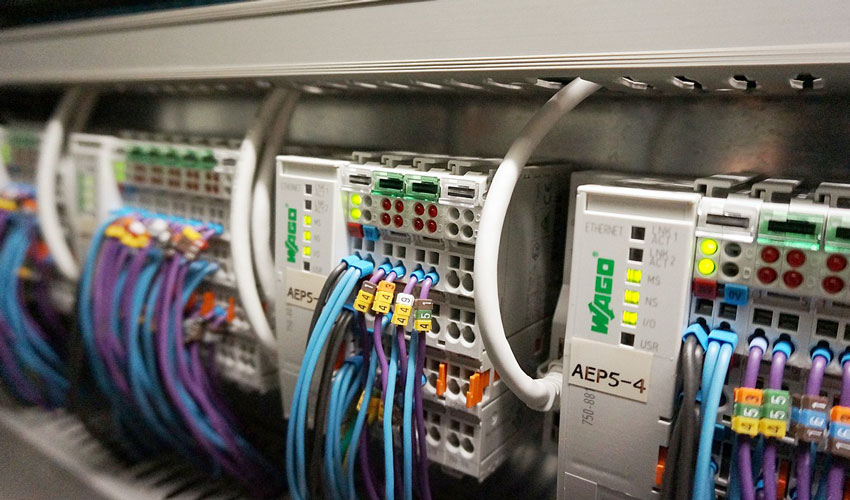
We rely on automated technology to carry out most of the important industrial activities in today’s world, ranging from producing power to weaving fabric in factories.
Fortunately, this technological advancement has led us to a point where we can innovate at unimaginable parameters. This is due to automation technology.
The constant progress of industrial advancement has brought forth an important invention known as the Programmable Logic Controller.
So, what exactly are a Programmable Logic Controller and PLC Training associated with it? How can these controllers assist us in managing the various operations needed in today’s world? Let us find out further!
What Is Programmable Control Logic?
A programmable logic controller is a small computer with inputs for data and outputs for sending and receiving commands. A PLC’s primary duty is to regulate a system’s operations using the underlying logic, as per its programming.
When it comes to automating a business’s most crucial procedures, PLCs are examples to rely on. A PLC receives inputs from automated data collection points and human input points like buttons and switches.
It then chooses whether to modify the output based on its programming. The outputs of a PLC can manage a wide range of machinery, including motors, solenoid valves, switchgear, safety shut-offs, and so much more.
PLCs continue to be a key component of many industrial control systems even in today’s time. They continue to be the world’s most widely utilised industrial control technology. Proficiency with PLCs is a basic prerequisite for a wide range of jobs, from engineers developing the system to electrical technicians maintaining it.
Working of Programmable Control Logic
The programmable logic controller gathers data from connected sensors and input devices, processes it and then initiates the necessary outputs in terms of its pre-programmed settings.
A PLC can readily monitor and record runtime data, such as operating temperature, machine productivity, and automatic start and stop procedures. As a result, PLCs are reliable and versatile manufacturing process control solutions for various applications.
Key Features of Programmable Control Logic
Some of the key features of the Programmable Control Application include the following:
- In addition to its association with various input and output devices, PLCs also need to link to other systems. For example, let’s assume how a user might need to export application data captured by the PLC to a Supervisory Control and Data Acquisition or SCADA, a system intended to track numerous connected devices. To simplify the connection between the PLC and other systems, a PLC offers a variety of communication ports and protocols.
- The CPU stores and processes data during the input and output modules; these link the PLC to the machinery. The I/O modules deliver data to the CPU and cause-specific outcomes. It should be noted that I/O can be combined to create the ideal configuration for a given application.
- To communicate with a PLC, users need a Human Machine Interface. Then, users can see PLC data in real-time using simple displays or big touchscreen screens as operator interfaces.
Advantages Of Using Programmable Control Logic
Let us check out a few points that discuss the various advantages of PLCs, or Programmable Logic Controls:
- A technology like PLC has undergone extensive testing and study. As a result, strong studies on various PLC types are readily available, as are in-depth guides for programming and integrating them.
- They are incredibly adaptable, and most PLC versions may be used to handle a range of systems and processes.
- Since PLCs have fewer parts, they are simpler to debug and require less downtime for maintenance.
- Programming PLCs is a rather simple process as they are excellent for firms that wish to reduce complexity and expenses because their programming languages are straightforward compared to those of other industrial control systems.
- PLCs come in a wide range of price ranges, including many basic types that are quite cheap and frequently used by small firms and start-ups.
The Bottom Line
Due to the current excitement surrounding Industry 4.0 and the industrial Internet of Things, PLCs will continue to gain popularity. In addition to that, PLCs will always be needed for operations because they provide web-based communication and so much more!
As a result, PLCs will consequently play a bigger role in modern machine automation.